在多循環測試的極限場景下,恒溫恒濕彎折試驗機的角度復位精度面臨更嚴峻考驗,但技術方案已構建起全維度的偏移防控體系。當設備在 - 60℃至 180℃的溫度沖擊環境中進行每秒 2 次的高頻彎折時,其角度控制精度仍能保持在 0.05° 以內,這得益于三層遞進式的精度保障機制。

在微觀磨損補償層面,設備采用的金剛石涂層彎折軸與碳化硅襯套形成自潤滑摩擦副,經 100 萬次循環測試后,表面磨損量僅為 0.2μm。配合內置的磨損量預測模型,系統可根據運行時間與環境參數,提前計算出可能的角度偏移量并進行預補償。某航空材料測試中,該技術使 20 萬次循環后的復位誤差穩定在 0.03°,較傳統金屬摩擦副降低 80% 的偏移風險。
動態應力釋放設計有效抵消了材料疲勞影響。彎折機構的彈性支撐組件采用鎳鈦合金記憶材料,在每 1000 次循環后會自動進行 0.5 秒的應力釋放動作,消除累積的殘余應力。同步采集的應變片數據顯示,這種主動釋放機制可使機構形變誤差從 0.04° 降至 0.015°。在柔性電路板的 180° 彎折測試中,該功能讓 10 萬次循環后的線路斷裂位置偏差控制在 0.1mm 范圍內。
智能學習算法構建了防護網。設備通過邊緣計算模塊實時分析近 1000 次的復位數據,建立角度偏移趨勢模型。當檢測到偏移量呈現 0.001°/ 千次的累積趨勢時,立即啟動伺服電機的相位微調。某消費電子實驗室的對比測試表明,啟用該算法后,20 萬次循環的角度總偏移量從 0.08° 壓縮至 0.025°,實現了真正意義上的長期零漂移運行。

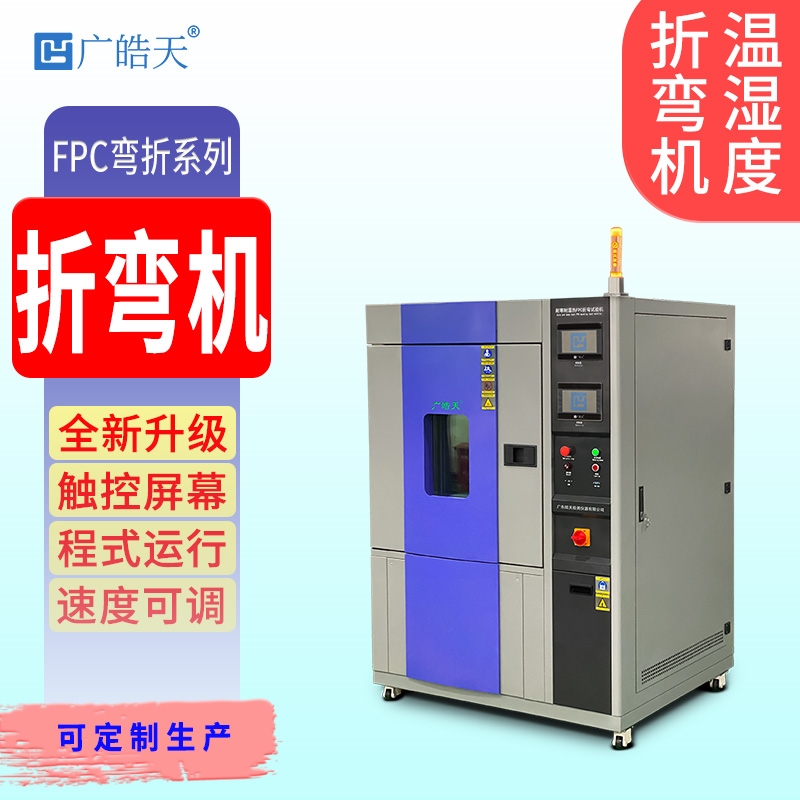
在半導體封裝引線的測試中,這種精準控制展現出價值。直徑僅 0.05mm 的金絲在 - 55℃至 125℃的溫度循環中進行 90° 彎折,設備通過上述三重機制,確保每次彎折的圓心位置偏差不超過 1μm,復現了芯片在溫度沖擊下的引線疲勞過程,為封裝可靠性設計提供了納米級精度的數據支撐。
可見,現代恒溫恒濕彎折試驗機已突破機械極限,通過材料、結構與算法的深度融合,在多循環測試的全生命周期內實現了近乎零偏移的控制精度,成為材料可靠性驗證的設備。